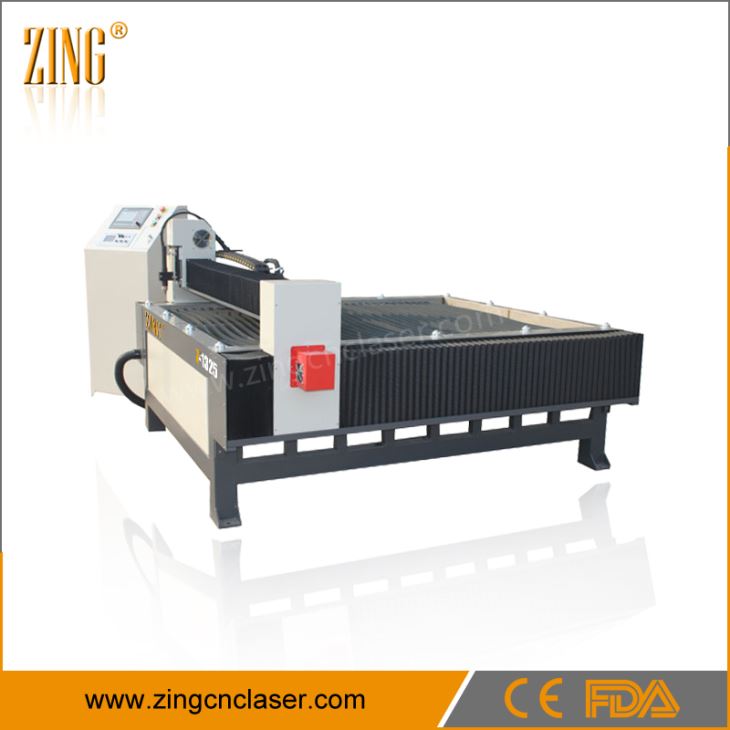
computerized plasma cutters
Do you require top-notch industrial plasma cutters, plasma metal cutters, or CNC plasma cutters? Look no further than Zing Company, an esteemed manufacturer and exporter in this field. Our range includes plasma CNC cutters and computerized plasma cutters, ensuring precision and efficiency in all...
Description
Do you require top-notch industrial plasma cutters, plasma metal cutters, or CNC plasma cutters? Look no further than Zing Company, an esteemed manufacturer and exporter in this field. Our range includes plasma CNC cutters and computerized plasma cutters, ensuring precision and efficiency in all your cutting needs. For more information about our cutting-edge machines, feel free to get in touch with us directly.
The industrial plasma cutter is characterized by its main technical parameters, which are essential in ensuring optimal performance. These parameters include the power supply voltage, the cutting capacity, the cutting speed, the power frequency, and the duty cycle. | ||
Equipment | Specification | |
Model | Z1325 | |
Effective area | 1300*2500mm | |
Max running speed | 9000mm/min | |
Running precision | ±0.4mm | |
Re-position decision | ±0.2mm | |
Cutting capacity | Depend on the plasma power source | |
Drive mode | Middle drive | |
Cutting torch number | 1 plasma |
The essential equipment of a plasma metal cutter includes a power supply, a plasma torch, and a gas system. These components work together to achieve efficient and precise metal cutting. | |
Equipment | Brand or origin |
Control system | Start-DSP Shaphon China |
Auto height control | XPTHC, China (100mm) |
X, Y drive | Hybrid servo driver and motor |
X, Y transmission | Taiwan import square |
Software | Fast CAM |
Flume | stainless steel flume |
Guard bar | Red pointer protect |
The process of separating materials using computerized plasma cutters is essential in various industries. These machines utilize a high-velocity jet of ionized gas, also known as plasma, to melt through metals and other materials. The precision and accuracy of plasma cutters make them ideal for cutting intricate shapes and designs. | |||
Parts | Equipment | Quantity | |
Control system | Control unit | 1 set | Start-DSP Shaphon China |
Accessories | 1 case | ||
Software | Programing Software | 1 set | Fast CAM(str) |
Servo system | X axis motor | 1 set | Hybrid servo motor and driver |
Y axis motor | 1 set | ||
Transformer | 1 set | ||
Mechanic Part | Host | 1 set | |
Linear tracks | 1 set | ||
Ball screw | 1 set | ||
Tackles | 1 set | ||
Towlines | 1 set | ||
Protective parts | 1 set | ||
Spray-print and other treatment | |||
Control cabinet |
Details Introduction of plasma cnc cutters: |
Samples of plasma cutter cnc: |
Send Inquiry
You Might Also Like